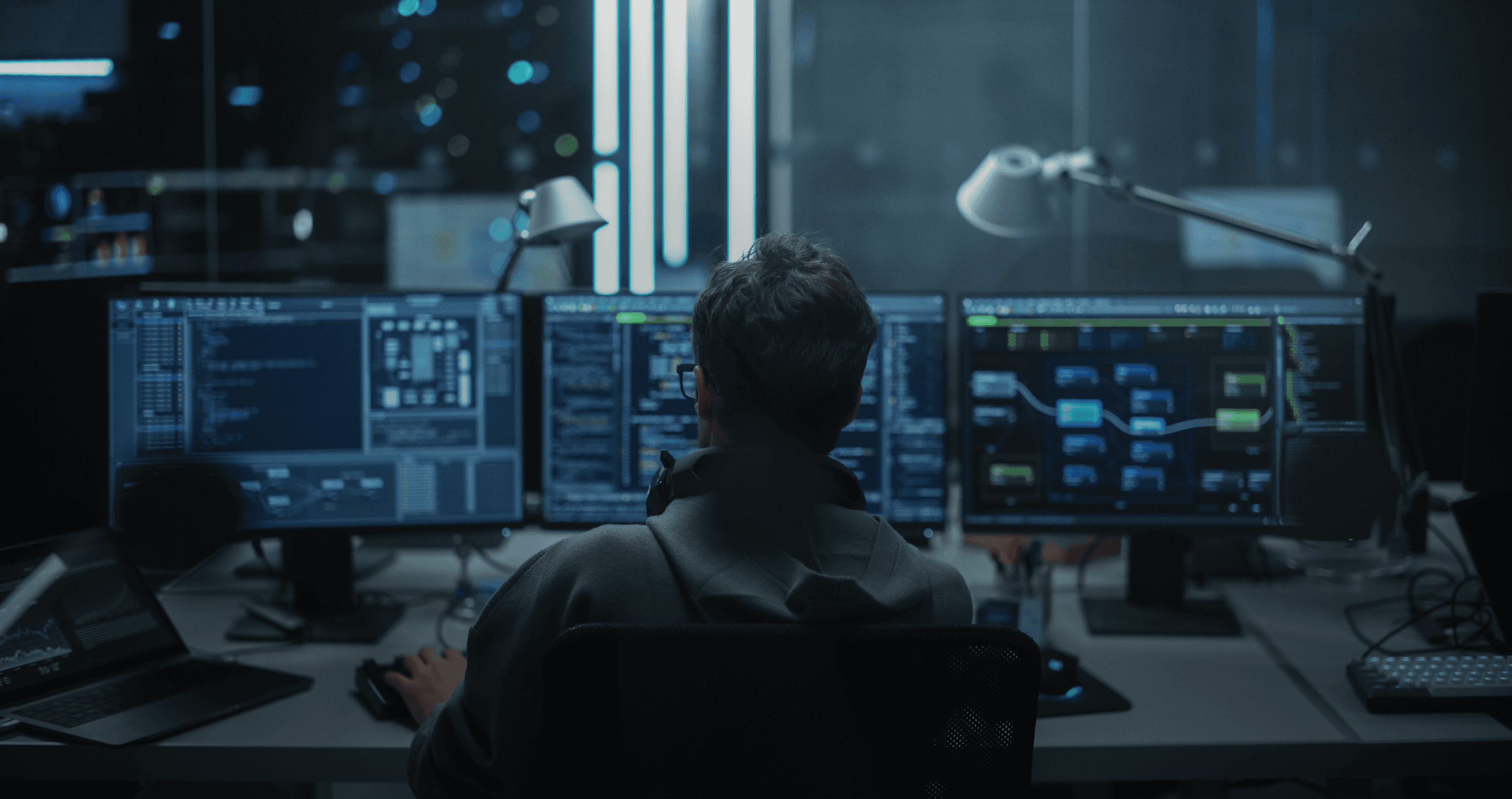
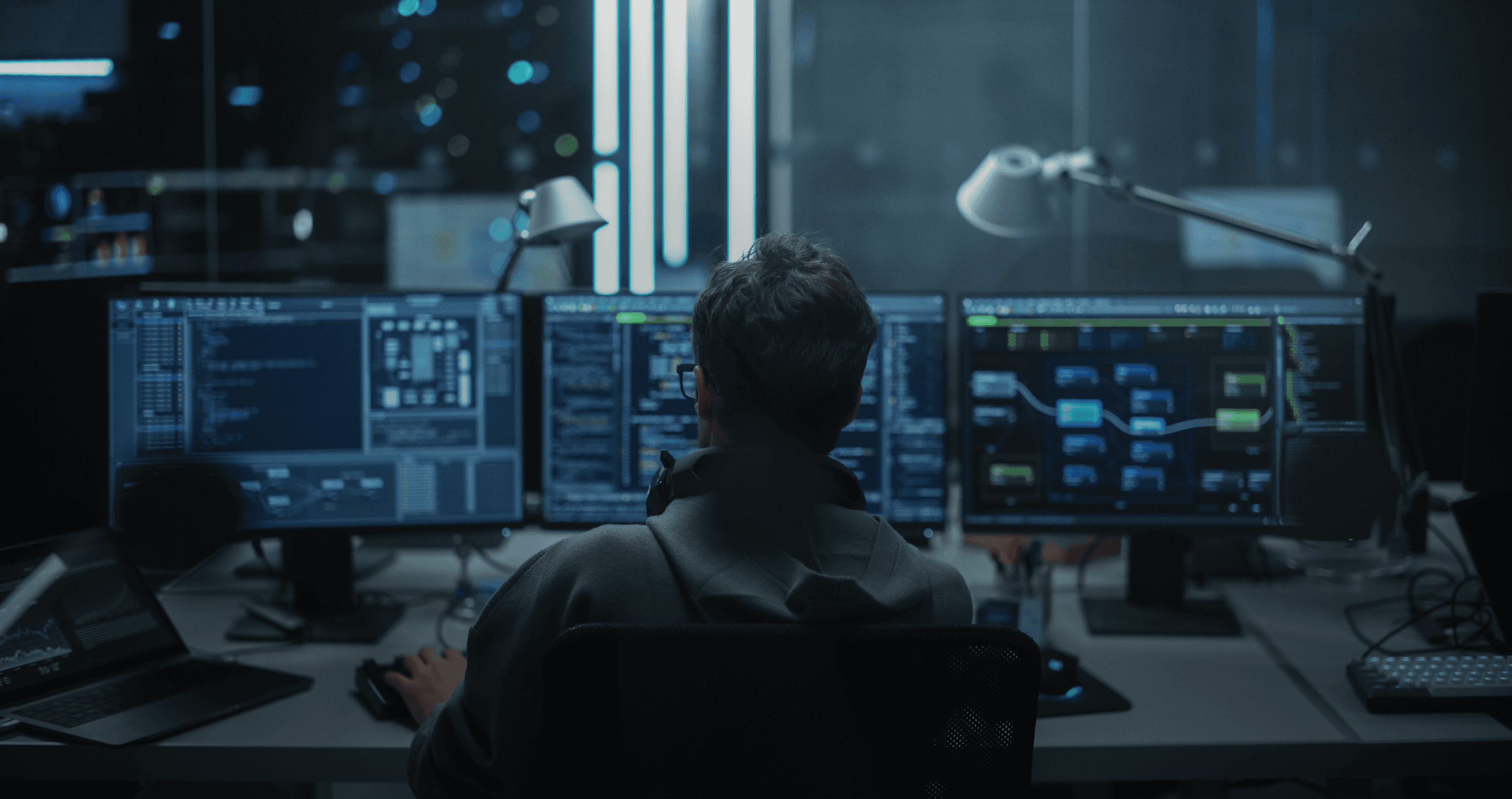
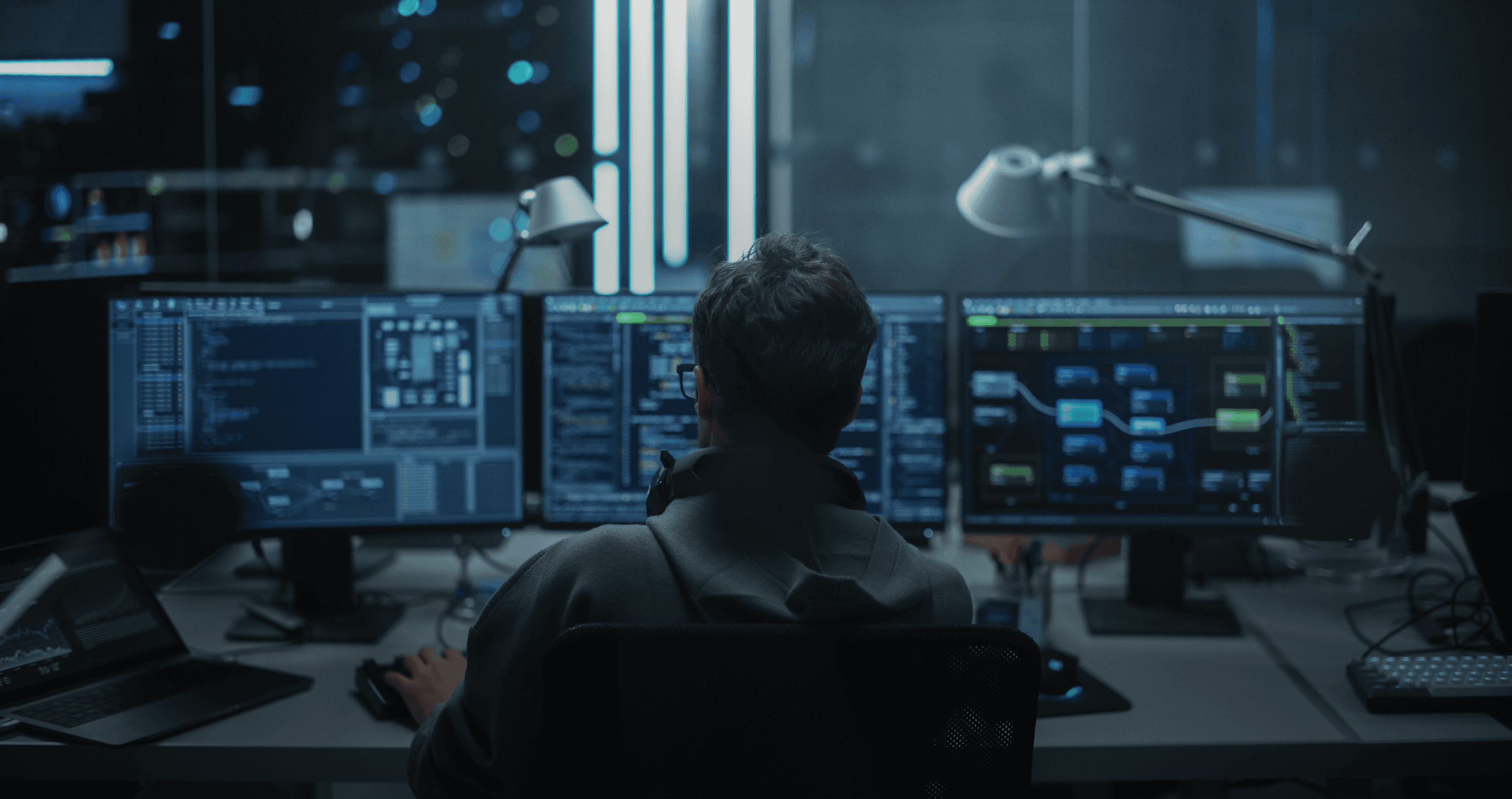
Learn from our clients' experiences
Learn from our clients' experiences
Learn from our clients' experiences
We've delivered projects across various industries and niches. Search below to discover a case study relevant to your business.
We've delivered projects across various industries and niches. Search below to discover a case study relevant to your business.
We've delivered projects across various industries and niches. Search below to discover a case study relevant to your business.
Our Experience
Find a case similar to yours
Uncover relevant case studies with our powerful search and tagging system.
Search…
Media & Entertainment
E-commerce
FinTech
Hospitality
Renewable Energy
Real Estate
Airlines
Logistics
Manufacturing
Data Analytics

Airlines
Cloud
AI
8 minutes to read
Airport Baggage Handling System: Engineering for Mission-Critical Reliability
A major Eastern European international airport, serving millions of passengers annually, faced a significant expansion challenge. The addition of a new terminal required a state-of-the-art baggage handling system that could operate flawlessly from day one.
Learn more

FinTech
QA
UI/UX Design
5 minutes to read
Digital audit platform
Brightgrove has partnered with a German-based company which provides Digital Audit Platform to 500+ audit, financial and professional firms. The main goal of the platform is to speed up the Balance Confirmation request process for Audit providers and their clients.
Learn more

Hospitality
AI
Microservices
4 minutes to read
5S Scenario Builder. Corporate Hotel Program Optimization
The strategic hotel selection process required processing vast amounts of historical booking data across thousands of hotels and evaluating hundreds of potential hotel combinations for each city.
Learn more

Data Analytics
Cloud
REST API
8 minutes to read
Coginiti—Data Analytics Management Software
Since 2012, Brightgrove has maintained an enduring partnership with Aginity (now Coginiti), the management company through multiple transformative phases.
Learn more

Manufacturing
IoT
Cloud
7 minutes to read
IoT Solution for Industrial Tools Manufacturer
Our client, a global leader in industrial tools and automotive components manufacturing, sought to integrate Internet of Things (IoT) capabilities into their product line, transforming traditional industrial tools into smart, connected devices.
Learn more

Renewable Energy
Cloud
Microservices
7 minutes to read
Cloud-Based Asset Management for Renewable Energy Plants
For this project, Meteocontrol wanted to develop a cloud-based asset management platform (mc Assetpilot) that could optimize renewable energy operations, streamline financial tracking, and enhance operational decision-making.
Learn more

Logistics
QA
REST API
6 minutes to read
PIN Mail AG. Leading German correspondence delivery company
Founded in 1999 in Berlin, PIN Mail AG is a leading German correspondence delivery company with over 1,300 employees.
Learn more

Logistics
Cloud
REST API
5 minutes to read
IoT-Connected Car Tracking Mobile Applications for Fleet Management
A leading German manufacturer of car tracking devices, specializing in onboard diagnostics (OBD) solutions, sought to enhance its vehicle tracking and trip logging capabilities through connected mobile apps.
Learn more

Manufacturing
REST API
Cloud
6 minutes to read
Legacy ERP System Redevelopment for an Industrial Equipment Manufacturer
When a leading German industrial equipment manufacturer found their 70-year legacy hampering growth, they turned to Brightgrove for a solution.
Learn more

Manufacturing
IoT
SAP
6 minutes to read
Machine Vision Solution for Industrial Manufacturing
The company aimed to standardize its software solutions across all business units, ensuring scalability, efficiency, and uniformity.
Learn more

Real Estate
SAP
Mobile
4 minutes to read
Promos—Real Estate CRM
A leading German real estate software company with a €32 million annual revenue and over two decades of market leadership faced the challenge of finding SAP developers who also understand mobile development.
Learn more

FinTech
Cloud
Microservices
5 minutes to read
UK-based payment solution provider expanding to continental Europe
Brightgrove has partnered with an ambitious UK-based company to extend their cloud-native payment solution platform.
Learn more

Hospitality
UI/UX Design
QA
5 minutes to read
Digital Transformation of Commission Collection for a Global Hotel Supplier
Our team was engaged by a global hotel supplier to implement the "Paywall" initiative – a comprehensive digital transformation of their commission collection process.
Learn more

Hospitality
REST API
Cloud
4 minutes to read
RESTification — Process Access to REST APIs for Partners
An organization undergoing modernization needs to manage and secure access to its REST APIs for external partners.
Learn more

Media & Entertainment
SaaS
Microservices
8 minutes to read
Planeta Kino Digital Transformation: A Multi-Platform Success Story
This comprehensive transformation involved modernizing multiple customer-facing platforms while maintaining business continuity for their cinemas network and premium viewing experiences.
Learn more

Hospitality
Cloud
Microservices
6 minutes to read
API-First Architecture Implementation for a Global Hospitality Tech Platform
The client faced critical scalability challenges during peak travel seasons, potentially risking up to €800K – €1M in lost bookings during high-demand periods. Their legacy booking system, built over 10 years ago, struggled to handle modern integration requirements.
Learn more

Real Estate
Cloud
Microservices
3 minutes to read
Real Estate platform Upgrade
The real estate platform serves as a backbone for the day-to-day real estate broker operations as well as provides overview and detailed reports on the past and current real estate market state.
Learn more

Hospitality
Cloud
UI/UX Design
6 minutes to read
Procurement Platform Interface Modernization from JSF to React
The HRS eRFP platform, also known as the HRS procurement or sourcing platform, is a comprehensive solution developed by HRS Group to streamline corporate hotel procurement processes.
Learn more
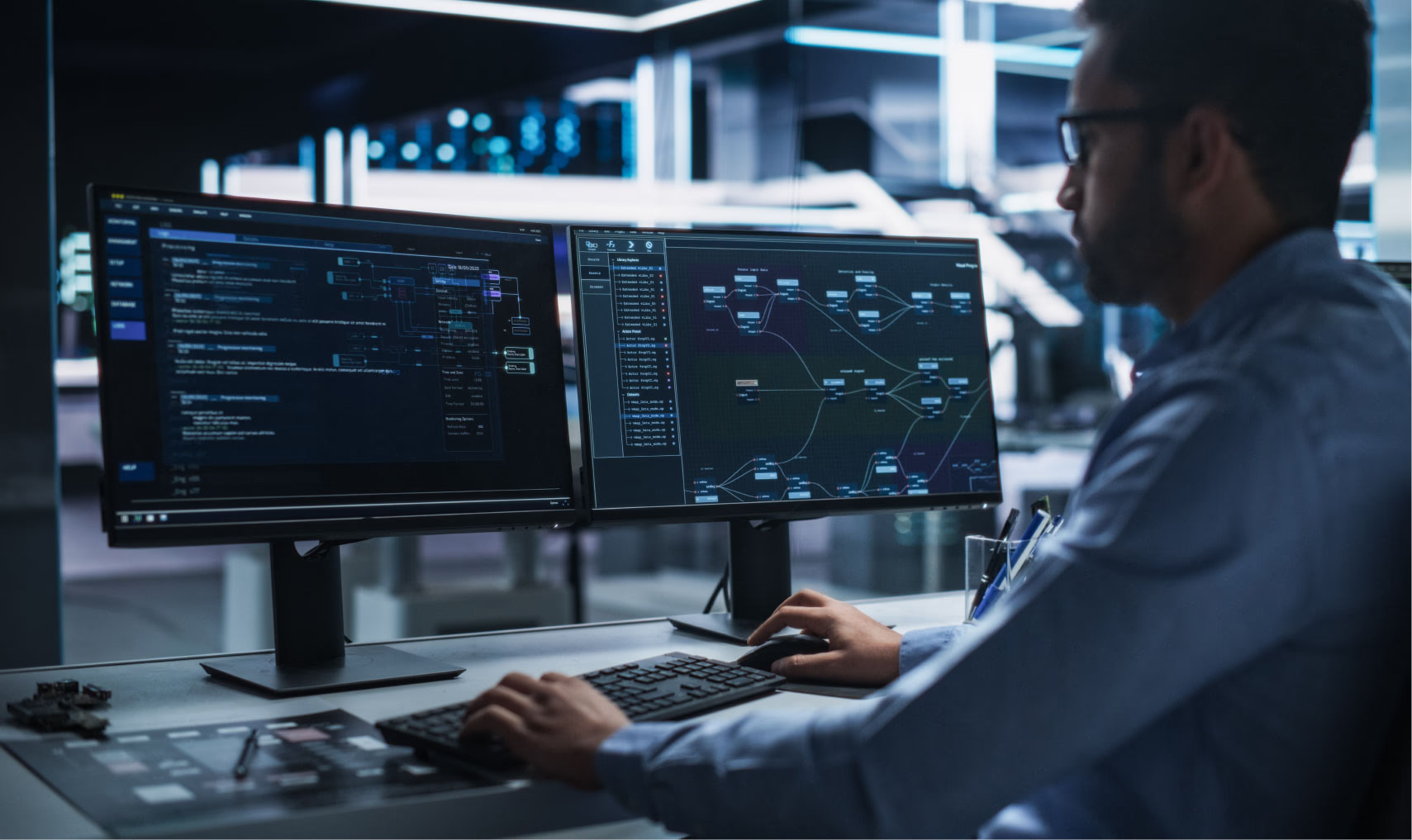
Hospitality
Cloud
AWS
5 minutes to read
Large North-American Travel Tech Booking Engine Modernization
An enterprise-scale leisure travel marketplace connecting travel agents with leisure-focused travel suppliers, facilitating research, marketing, and selling of vacations in the USA and Canada.
Learn more

Renewable Energy
UI/UX Design
Microservices
6 minutes to read
From Raw Data to Interactive Visualization for Solar Monitoring System
In 2012, solar monitoring systems were primarily data-driven, offering raw data outputs with minimal visual representation or integration. Operators struggled with scattered screens and single-purpose tools.
Learn more

Hospitality
FinTech
Cloud
8 minutes to read
Successful integration cases across different domains
The following use cases demonstrate our ability to tackle integration challenges of varying complexity across different business domains.
Learn more

Hospitality
Microservices
Cloud
5 minutes to read
Solving Integration Problems in Travel Tech
We partnered with a global travel technology company to overhaul their fragmented systems through advanced integration services.
Learn more

Hospitality
Cloud
SaaS
4 minutes to read
Collaborative SaaS Transformation of a Global Travel Technology Platform
Faced with rising AWS costs, a top-three European hotel portal and global business travel leader required a comprehensive cost optimization strategy
Learn more

Hospitality
Cloud
AWS
3 minutes to read
Cloud transformation—AWS cost optimization
Global hotel solutions provider, ranking among the top three hotel portals in Europe faced challenges with escalating AWS costs and had to define and implement a comprehensive cost optimization strategy.
Learn more

Hospitality
Google Cloud
Azure
3 minutes to read
Cloud migration—cloud to cloud—Lift & shift—GCP to Azure
On our tech exploration journey, we discovered an innovator rooted in a thriving metropolis, a beacon of forward-thinking and adaptability in the tech realm. Their location, pulsating with life and dynamism, seemed symbolic of their approach: always moving, always evolving.
Learn more

FinTech
Microservices
AWS
3 minutes to read
Cloud migration—cloud to multicloud
In a dynamic marketplace, this platform stands out, offering a seamless, enriching shopping experience.
Learn more

Media & Entertainment
Cloud
AWS
4 minutes to read
Cloud migration—monolith to cloud
Free ad-supported streaming television (FAST) service owned and operated by the Paramount Streaming division of Paramount Global.
Learn more

Hospitality
Cloud
Microservices
3 minutes to read
HRS GROUP—a global tech company focusing on business travel
HRS Group is a global tech company focusing on business travel, ranking among the top three hotel portals in Europe and as a market leader in the global business travel sector.
Learn more

E-commerce
UI/UX Design
Computer Vision
4 minutes to read
AI Powered Amazon Recommendation Engine
The client needed a smart solution that could analyze thousands of Amazon marketplace products to identify optimization opportunities.
Learn more
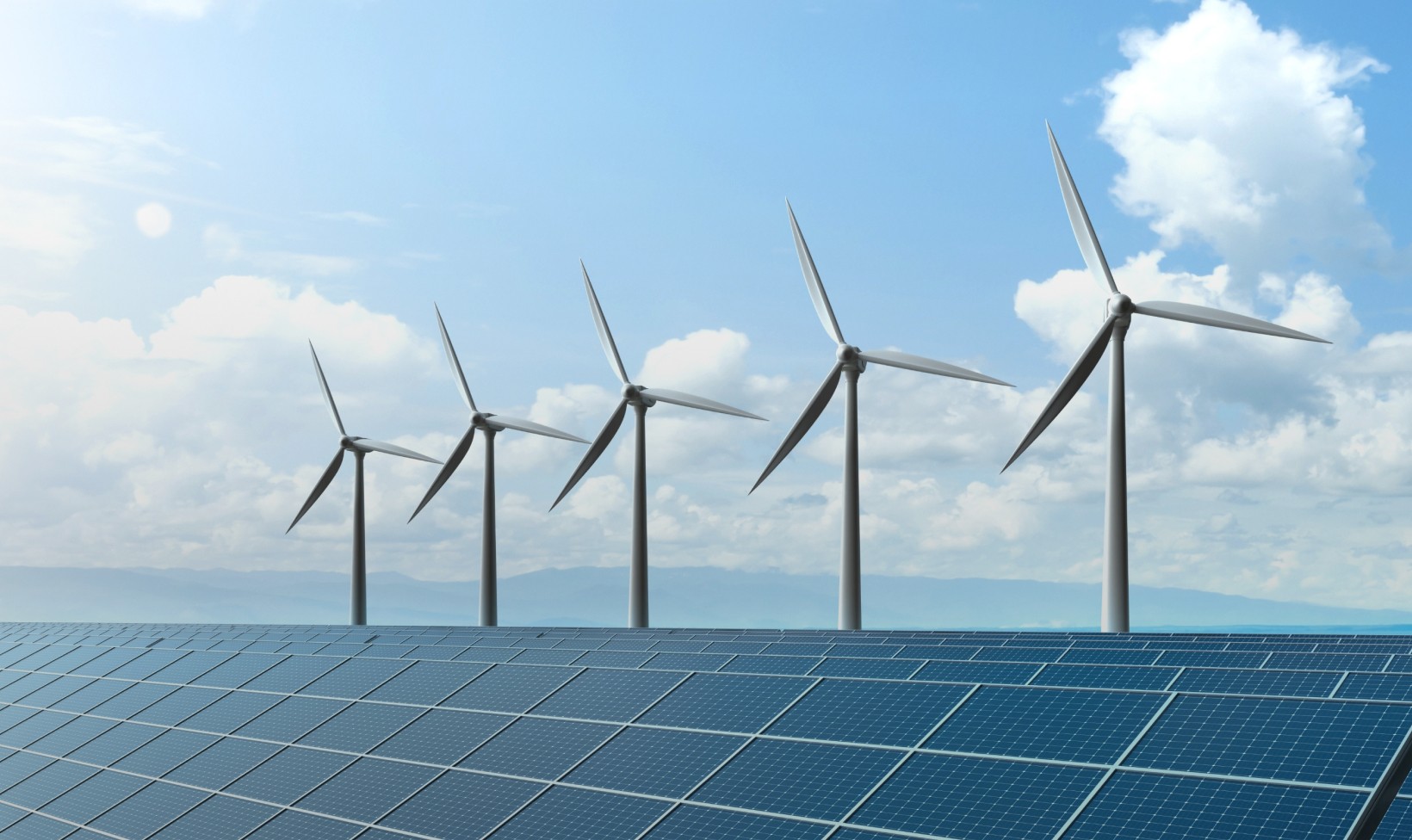
Renewable Energy
SaaS
Google Cloud
4 minutes to read
CerQlar—renewable energy trading and certification platform
In 2021, we partnered up with CerQlar, a Dutch company setting new energy attribute certificate trading standards in Europe.
Learn more

Real Estate
AI
Cloud
4 minutes to read
Modernizing New York's Real Estate Technology Platform
In 2014, we started one of our most long-running projects with a client, a US real estate agency turned digital leader in its industry.
Learn more
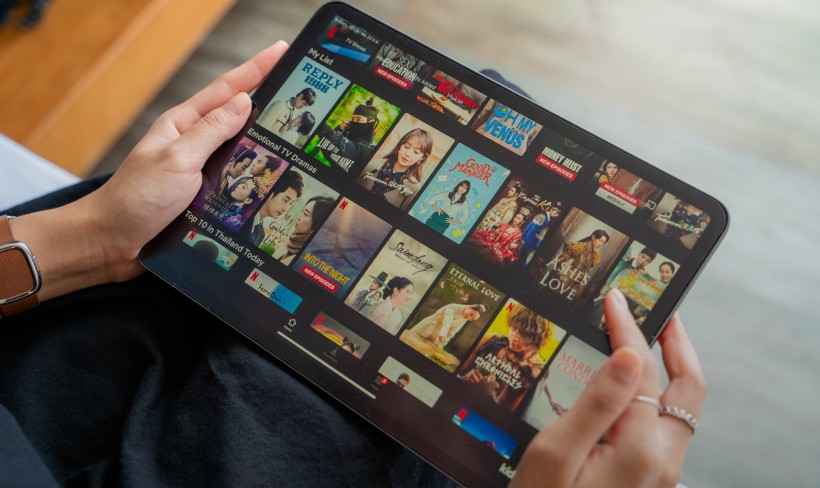
Media & Entertainment
OTT Platform
Ad Tech
5 minutes to read
Pluto TV—a free streaming TV service owned by Paramount Global
In 2017, we kicked off our journey with Pluto.tv by bringing on board top-notch engineers to kickstart our development teams and lay the groundwork for Pluto.tv's bright future.
Learn more
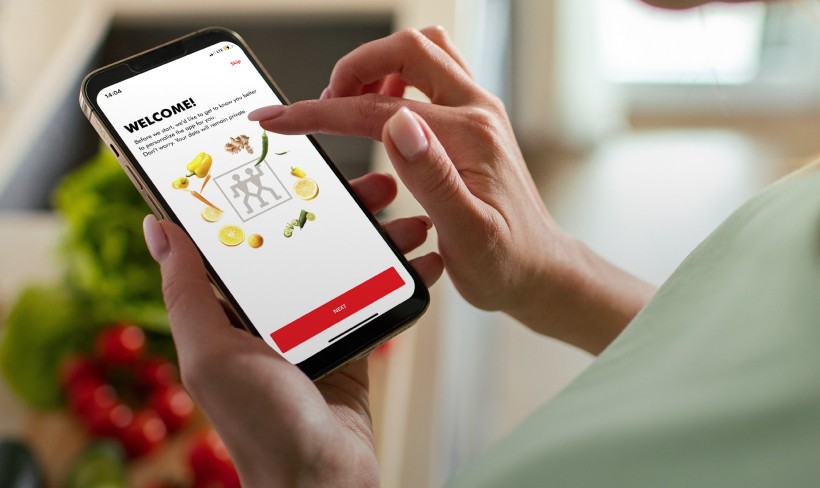
Manufacturing
E-commerce
IoT
4 minutes to read
ZWILLING—a renowned brand in crafting high-quality kitchenware
In May 2021, we began working with ZWILLING to develop stable and user-friendly native Android and iOS applications for their innovation department.
Learn more
Find a case similar to yours
Uncover relevant case studies with our powerful search and tagging system.
Search…
Media & Entertainment
E-commerce
FinTech
Hospitality
Renewable Energy
Real Estate
Airlines
Logistics
Manufacturing
Data Analytics

Airlines
Cloud
AI
8 minutes to read
Airport Baggage Handling System: Engineering for Mission-Critical Reliability
A major Eastern European international airport, serving millions of passengers annually, faced a significant expansion challenge. The addition of a new terminal required a state-of-the-art baggage handling system that could operate flawlessly from day one.
Learn more

FinTech
QA
UI/UX Design
5 minutes to read
Digital audit platform
Brightgrove has partnered with a German-based company which provides Digital Audit Platform to 500+ audit, financial and professional firms. The main goal of the platform is to speed up the Balance Confirmation request process for Audit providers and their clients.
Learn more

Hospitality
AI
Microservices
4 minutes to read
5S Scenario Builder. Corporate Hotel Program Optimization
The strategic hotel selection process required processing vast amounts of historical booking data across thousands of hotels and evaluating hundreds of potential hotel combinations for each city.
Learn more

Data Analytics
Cloud
REST API
8 minutes to read
Coginiti—Data Analytics Management Software
Since 2012, Brightgrove has maintained an enduring partnership with Aginity (now Coginiti), the management company through multiple transformative phases.
Learn more

Manufacturing
IoT
Cloud
7 minutes to read
IoT Solution for Industrial Tools Manufacturer
Our client, a global leader in industrial tools and automotive components manufacturing, sought to integrate Internet of Things (IoT) capabilities into their product line, transforming traditional industrial tools into smart, connected devices.
Learn more

Renewable Energy
Cloud
Microservices
7 minutes to read
Cloud-Based Asset Management for Renewable Energy Plants
For this project, Meteocontrol wanted to develop a cloud-based asset management platform (mc Assetpilot) that could optimize renewable energy operations, streamline financial tracking, and enhance operational decision-making.
Learn more

Logistics
QA
REST API
6 minutes to read
PIN Mail AG. Leading German correspondence delivery company
Founded in 1999 in Berlin, PIN Mail AG is a leading German correspondence delivery company with over 1,300 employees.
Learn more

Logistics
Cloud
REST API
5 minutes to read
IoT-Connected Car Tracking Mobile Applications for Fleet Management
A leading German manufacturer of car tracking devices, specializing in onboard diagnostics (OBD) solutions, sought to enhance its vehicle tracking and trip logging capabilities through connected mobile apps.
Learn more

Manufacturing
REST API
Cloud
6 minutes to read
Legacy ERP System Redevelopment for an Industrial Equipment Manufacturer
When a leading German industrial equipment manufacturer found their 70-year legacy hampering growth, they turned to Brightgrove for a solution.
Learn more

Manufacturing
IoT
SAP
6 minutes to read
Machine Vision Solution for Industrial Manufacturing
The company aimed to standardize its software solutions across all business units, ensuring scalability, efficiency, and uniformity.
Learn more

Real Estate
SAP
Mobile
4 minutes to read
Promos—Real Estate CRM
A leading German real estate software company with a €32 million annual revenue and over two decades of market leadership faced the challenge of finding SAP developers who also understand mobile development.
Learn more

FinTech
Cloud
Microservices
5 minutes to read
UK-based payment solution provider expanding to continental Europe
Brightgrove has partnered with an ambitious UK-based company to extend their cloud-native payment solution platform.
Learn more

Hospitality
UI/UX Design
QA
5 minutes to read
Digital Transformation of Commission Collection for a Global Hotel Supplier
Our team was engaged by a global hotel supplier to implement the "Paywall" initiative – a comprehensive digital transformation of their commission collection process.
Learn more

Hospitality
REST API
Cloud
4 minutes to read
RESTification — Process Access to REST APIs for Partners
An organization undergoing modernization needs to manage and secure access to its REST APIs for external partners.
Learn more

Media & Entertainment
SaaS
Microservices
8 minutes to read
Planeta Kino Digital Transformation: A Multi-Platform Success Story
This comprehensive transformation involved modernizing multiple customer-facing platforms while maintaining business continuity for their cinemas network and premium viewing experiences.
Learn more

Hospitality
Cloud
Microservices
6 minutes to read
API-First Architecture Implementation for a Global Hospitality Tech Platform
The client faced critical scalability challenges during peak travel seasons, potentially risking up to €800K – €1M in lost bookings during high-demand periods. Their legacy booking system, built over 10 years ago, struggled to handle modern integration requirements.
Learn more

Real Estate
Cloud
Microservices
3 minutes to read
Real Estate platform Upgrade
The real estate platform serves as a backbone for the day-to-day real estate broker operations as well as provides overview and detailed reports on the past and current real estate market state.
Learn more

Hospitality
Cloud
UI/UX Design
6 minutes to read
Procurement Platform Interface Modernization from JSF to React
The HRS eRFP platform, also known as the HRS procurement or sourcing platform, is a comprehensive solution developed by HRS Group to streamline corporate hotel procurement processes.
Learn more
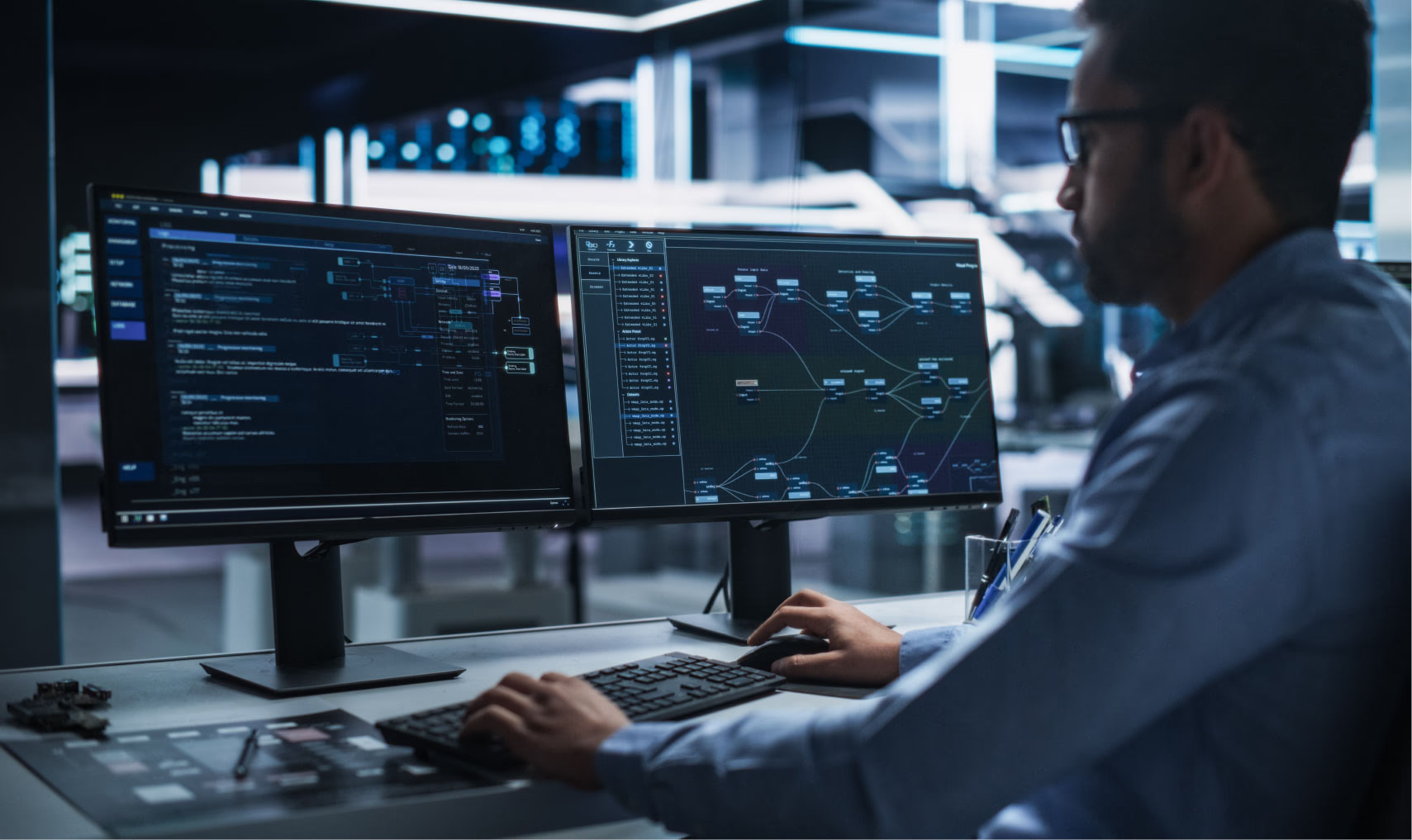
Hospitality
Cloud
AWS
5 minutes to read
Large North-American Travel Tech Booking Engine Modernization
An enterprise-scale leisure travel marketplace connecting travel agents with leisure-focused travel suppliers, facilitating research, marketing, and selling of vacations in the USA and Canada.
Learn more

Renewable Energy
UI/UX Design
Microservices
6 minutes to read
From Raw Data to Interactive Visualization for Solar Monitoring System
In 2012, solar monitoring systems were primarily data-driven, offering raw data outputs with minimal visual representation or integration. Operators struggled with scattered screens and single-purpose tools.
Learn more

Hospitality
FinTech
Cloud
8 minutes to read
Successful integration cases across different domains
The following use cases demonstrate our ability to tackle integration challenges of varying complexity across different business domains.
Learn more

Hospitality
Microservices
Cloud
5 minutes to read
Solving Integration Problems in Travel Tech
We partnered with a global travel technology company to overhaul their fragmented systems through advanced integration services.
Learn more

Hospitality
Cloud
SaaS
4 minutes to read
Collaborative SaaS Transformation of a Global Travel Technology Platform
Faced with rising AWS costs, a top-three European hotel portal and global business travel leader required a comprehensive cost optimization strategy
Learn more

Hospitality
Cloud
AWS
3 minutes to read
Cloud transformation—AWS cost optimization
Global hotel solutions provider, ranking among the top three hotel portals in Europe faced challenges with escalating AWS costs and had to define and implement a comprehensive cost optimization strategy.
Learn more

Hospitality
Google Cloud
Azure
3 minutes to read
Cloud migration—cloud to cloud—Lift & shift—GCP to Azure
On our tech exploration journey, we discovered an innovator rooted in a thriving metropolis, a beacon of forward-thinking and adaptability in the tech realm. Their location, pulsating with life and dynamism, seemed symbolic of their approach: always moving, always evolving.
Learn more

FinTech
Microservices
AWS
3 minutes to read
Cloud migration—cloud to multicloud
In a dynamic marketplace, this platform stands out, offering a seamless, enriching shopping experience.
Learn more

Media & Entertainment
Cloud
AWS
4 minutes to read
Cloud migration—monolith to cloud
Free ad-supported streaming television (FAST) service owned and operated by the Paramount Streaming division of Paramount Global.
Learn more

Hospitality
Cloud
Microservices
3 minutes to read
HRS GROUP—a global tech company focusing on business travel
HRS Group is a global tech company focusing on business travel, ranking among the top three hotel portals in Europe and as a market leader in the global business travel sector.
Learn more

E-commerce
UI/UX Design
Computer Vision
4 minutes to read
AI Powered Amazon Recommendation Engine
The client needed a smart solution that could analyze thousands of Amazon marketplace products to identify optimization opportunities.
Learn more
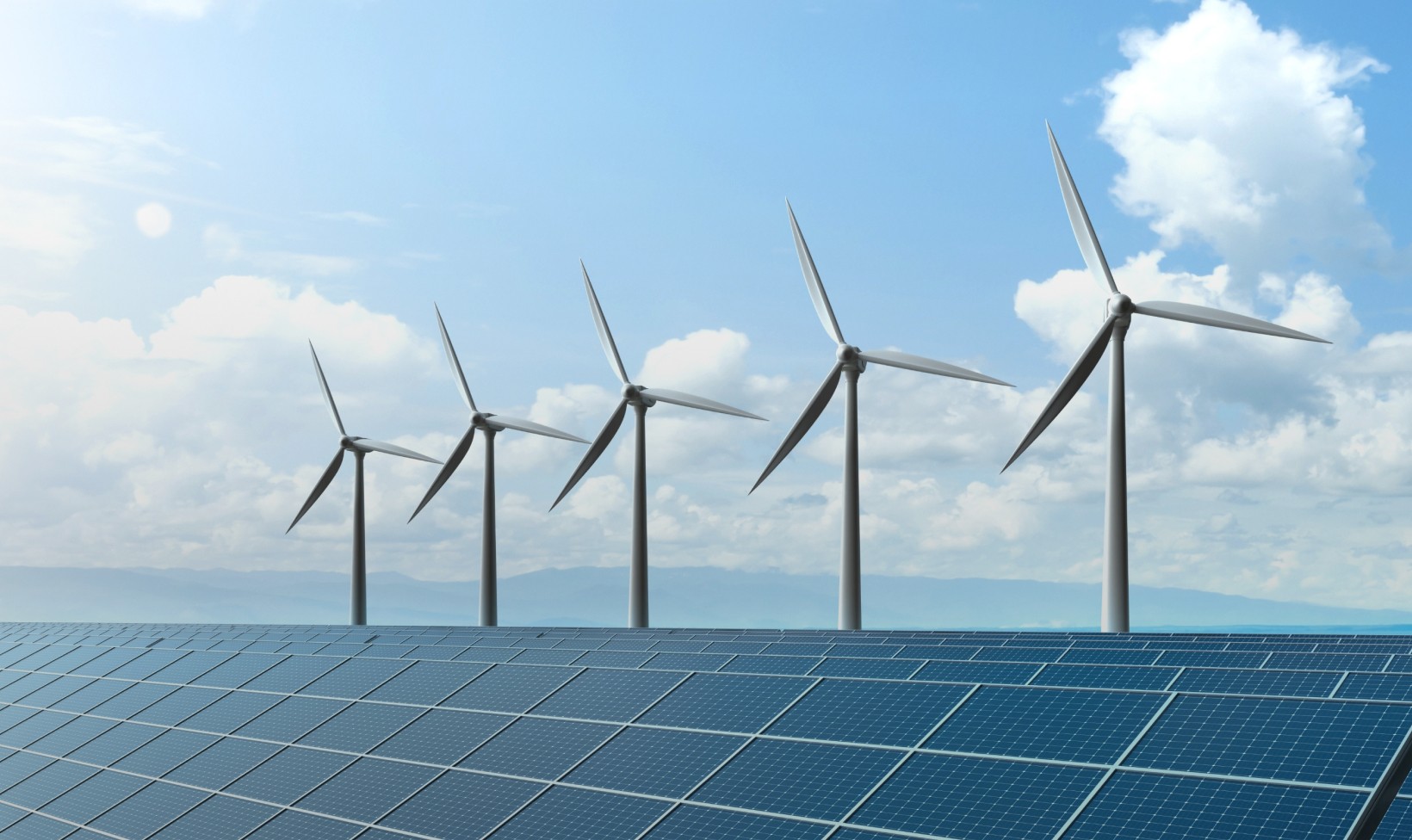
Renewable Energy
SaaS
Google Cloud
4 minutes to read
CerQlar—renewable energy trading and certification platform
In 2021, we partnered up with CerQlar, a Dutch company setting new energy attribute certificate trading standards in Europe.
Learn more

Real Estate
AI
Cloud
4 minutes to read
Modernizing New York's Real Estate Technology Platform
In 2014, we started one of our most long-running projects with a client, a US real estate agency turned digital leader in its industry.
Learn more
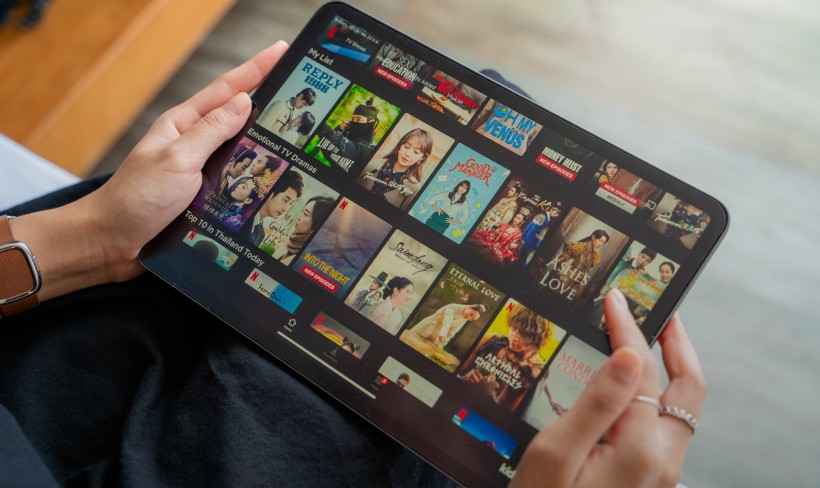
Media & Entertainment
OTT Platform
Ad Tech
5 minutes to read
Pluto TV—a free streaming TV service owned by Paramount Global
In 2017, we kicked off our journey with Pluto.tv by bringing on board top-notch engineers to kickstart our development teams and lay the groundwork for Pluto.tv's bright future.
Learn more
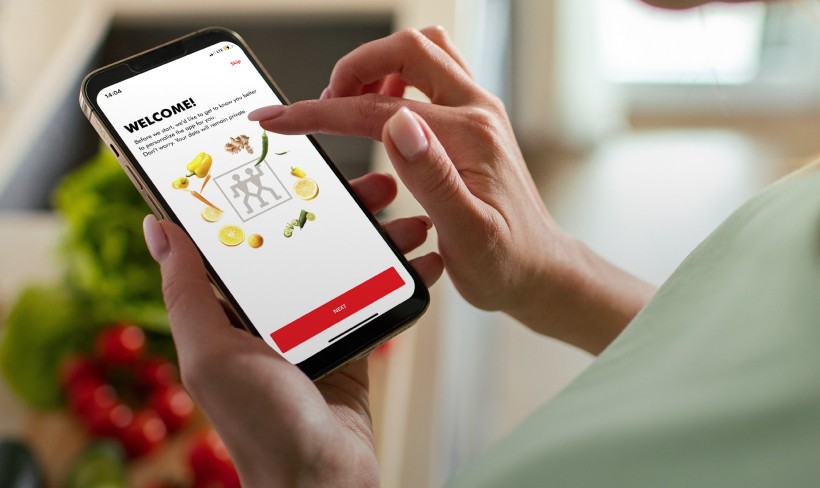
Manufacturing
E-commerce
IoT
4 minutes to read
ZWILLING—a renowned brand in crafting high-quality kitchenware
In May 2021, we began working with ZWILLING to develop stable and user-friendly native Android and iOS applications for their innovation department.
Learn more
Find a case similar to yours
Uncover relevant case studies with our powerful search and tagging system.
Search…
Media & Entertainment
E-commerce
FinTech
Hospitality
Renewable Energy
Real Estate
Airlines
Logistics
Manufacturing
Data Analytics

Airlines
Cloud
AI
8 minutes to read
Airport Baggage Handling System: Engineering for Mission-Critical Reliability
A major Eastern European international airport, serving millions of passengers annually, faced a significant expansion challenge. The addition of a new terminal required a state-of-the-art baggage handling system that could operate flawlessly from day one.
Learn more

FinTech
QA
UI/UX Design
5 minutes to read
Digital audit platform
Brightgrove has partnered with a German-based company which provides Digital Audit Platform to 500+ audit, financial and professional firms. The main goal of the platform is to speed up the Balance Confirmation request process for Audit providers and their clients.
Learn more

Hospitality
AI
Microservices
4 minutes to read
5S Scenario Builder. Corporate Hotel Program Optimization
The strategic hotel selection process required processing vast amounts of historical booking data across thousands of hotels and evaluating hundreds of potential hotel combinations for each city.
Learn more

Data Analytics
Cloud
REST API
8 minutes to read
Coginiti—Data Analytics Management Software
Since 2012, Brightgrove has maintained an enduring partnership with Aginity (now Coginiti), the management company through multiple transformative phases.
Learn more

Manufacturing
IoT
Cloud
7 minutes to read
IoT Solution for Industrial Tools Manufacturer
Our client, a global leader in industrial tools and automotive components manufacturing, sought to integrate Internet of Things (IoT) capabilities into their product line, transforming traditional industrial tools into smart, connected devices.
Learn more

Renewable Energy
Cloud
Microservices
7 minutes to read
Cloud-Based Asset Management for Renewable Energy Plants
For this project, Meteocontrol wanted to develop a cloud-based asset management platform (mc Assetpilot) that could optimize renewable energy operations, streamline financial tracking, and enhance operational decision-making.
Learn more

Logistics
QA
REST API
6 minutes to read
PIN Mail AG. Leading German correspondence delivery company
Founded in 1999 in Berlin, PIN Mail AG is a leading German correspondence delivery company with over 1,300 employees.
Learn more

Logistics
Cloud
REST API
5 minutes to read
IoT-Connected Car Tracking Mobile Applications for Fleet Management
A leading German manufacturer of car tracking devices, specializing in onboard diagnostics (OBD) solutions, sought to enhance its vehicle tracking and trip logging capabilities through connected mobile apps.
Learn more

Manufacturing
REST API
Cloud
6 minutes to read
Legacy ERP System Redevelopment for an Industrial Equipment Manufacturer
When a leading German industrial equipment manufacturer found their 70-year legacy hampering growth, they turned to Brightgrove for a solution.
Learn more

Manufacturing
IoT
SAP
6 minutes to read
Machine Vision Solution for Industrial Manufacturing
The company aimed to standardize its software solutions across all business units, ensuring scalability, efficiency, and uniformity.
Learn more

Real Estate
SAP
Mobile
4 minutes to read
Promos—Real Estate CRM
A leading German real estate software company with a €32 million annual revenue and over two decades of market leadership faced the challenge of finding SAP developers who also understand mobile development.
Learn more

FinTech
Cloud
Microservices
5 minutes to read
UK-based payment solution provider expanding to continental Europe
Brightgrove has partnered with an ambitious UK-based company to extend their cloud-native payment solution platform.
Learn more

Hospitality
UI/UX Design
QA
5 minutes to read
Digital Transformation of Commission Collection for a Global Hotel Supplier
Our team was engaged by a global hotel supplier to implement the "Paywall" initiative – a comprehensive digital transformation of their commission collection process.
Learn more

Hospitality
REST API
Cloud
4 minutes to read
RESTification — Process Access to REST APIs for Partners
An organization undergoing modernization needs to manage and secure access to its REST APIs for external partners.
Learn more

Media & Entertainment
SaaS
Microservices
8 minutes to read
Planeta Kino Digital Transformation: A Multi-Platform Success Story
This comprehensive transformation involved modernizing multiple customer-facing platforms while maintaining business continuity for their cinemas network and premium viewing experiences.
Learn more

Hospitality
Cloud
Microservices
6 minutes to read
API-First Architecture Implementation for a Global Hospitality Tech Platform
The client faced critical scalability challenges during peak travel seasons, potentially risking up to €800K – €1M in lost bookings during high-demand periods. Their legacy booking system, built over 10 years ago, struggled to handle modern integration requirements.
Learn more

Real Estate
Cloud
Microservices
3 minutes to read
Real Estate platform Upgrade
The real estate platform serves as a backbone for the day-to-day real estate broker operations as well as provides overview and detailed reports on the past and current real estate market state.
Learn more

Hospitality
Cloud
UI/UX Design
6 minutes to read
Procurement Platform Interface Modernization from JSF to React
The HRS eRFP platform, also known as the HRS procurement or sourcing platform, is a comprehensive solution developed by HRS Group to streamline corporate hotel procurement processes.
Learn more
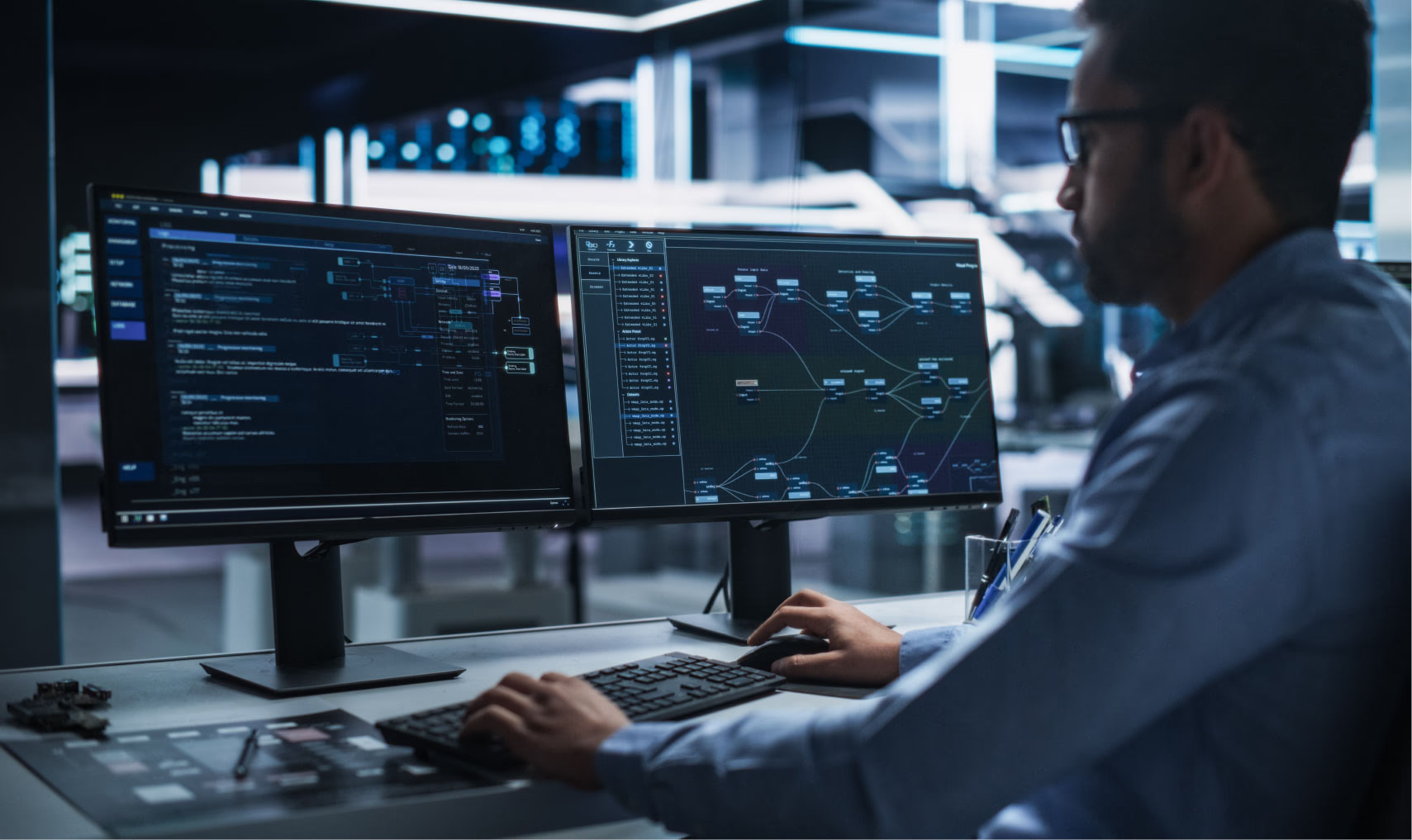
Hospitality
Cloud
AWS
5 minutes to read
Large North-American Travel Tech Booking Engine Modernization
An enterprise-scale leisure travel marketplace connecting travel agents with leisure-focused travel suppliers, facilitating research, marketing, and selling of vacations in the USA and Canada.
Learn more

Renewable Energy
UI/UX Design
Microservices
6 minutes to read
From Raw Data to Interactive Visualization for Solar Monitoring System
In 2012, solar monitoring systems were primarily data-driven, offering raw data outputs with minimal visual representation or integration. Operators struggled with scattered screens and single-purpose tools.
Learn more

Hospitality
FinTech
Cloud
8 minutes to read
Successful integration cases across different domains
The following use cases demonstrate our ability to tackle integration challenges of varying complexity across different business domains.
Learn more

Hospitality
Microservices
Cloud
5 minutes to read
Solving Integration Problems in Travel Tech
We partnered with a global travel technology company to overhaul their fragmented systems through advanced integration services.
Learn more

Hospitality
Cloud
SaaS
4 minutes to read
Collaborative SaaS Transformation of a Global Travel Technology Platform
Faced with rising AWS costs, a top-three European hotel portal and global business travel leader required a comprehensive cost optimization strategy
Learn more

Hospitality
Cloud
AWS
3 minutes to read
Cloud transformation—AWS cost optimization
Global hotel solutions provider, ranking among the top three hotel portals in Europe faced challenges with escalating AWS costs and had to define and implement a comprehensive cost optimization strategy.
Learn more

Hospitality
Google Cloud
Azure
3 minutes to read
Cloud migration—cloud to cloud—Lift & shift—GCP to Azure
On our tech exploration journey, we discovered an innovator rooted in a thriving metropolis, a beacon of forward-thinking and adaptability in the tech realm. Their location, pulsating with life and dynamism, seemed symbolic of their approach: always moving, always evolving.
Learn more

FinTech
Microservices
AWS
3 minutes to read
Cloud migration—cloud to multicloud
In a dynamic marketplace, this platform stands out, offering a seamless, enriching shopping experience.
Learn more

Media & Entertainment
Cloud
AWS
4 minutes to read
Cloud migration—monolith to cloud
Free ad-supported streaming television (FAST) service owned and operated by the Paramount Streaming division of Paramount Global.
Learn more

Hospitality
Cloud
Microservices
3 minutes to read
HRS GROUP—a global tech company focusing on business travel
HRS Group is a global tech company focusing on business travel, ranking among the top three hotel portals in Europe and as a market leader in the global business travel sector.
Learn more

E-commerce
UI/UX Design
Computer Vision
4 minutes to read
AI Powered Amazon Recommendation Engine
The client needed a smart solution that could analyze thousands of Amazon marketplace products to identify optimization opportunities.
Learn more
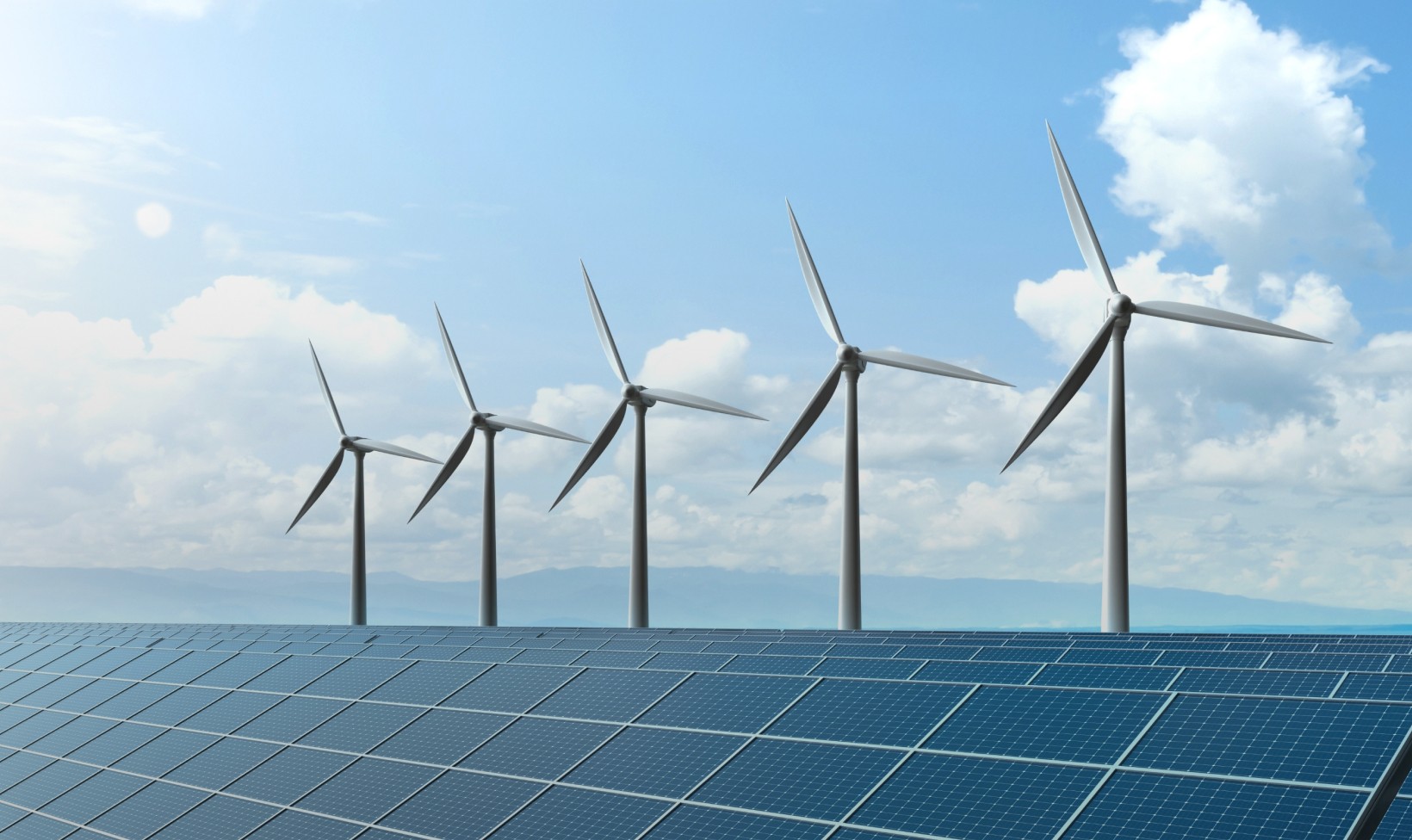
Renewable Energy
SaaS
Google Cloud
4 minutes to read
CerQlar—renewable energy trading and certification platform
In 2021, we partnered up with CerQlar, a Dutch company setting new energy attribute certificate trading standards in Europe.
Learn more

Real Estate
AI
Cloud
4 minutes to read
Modernizing New York's Real Estate Technology Platform
In 2014, we started one of our most long-running projects with a client, a US real estate agency turned digital leader in its industry.
Learn more
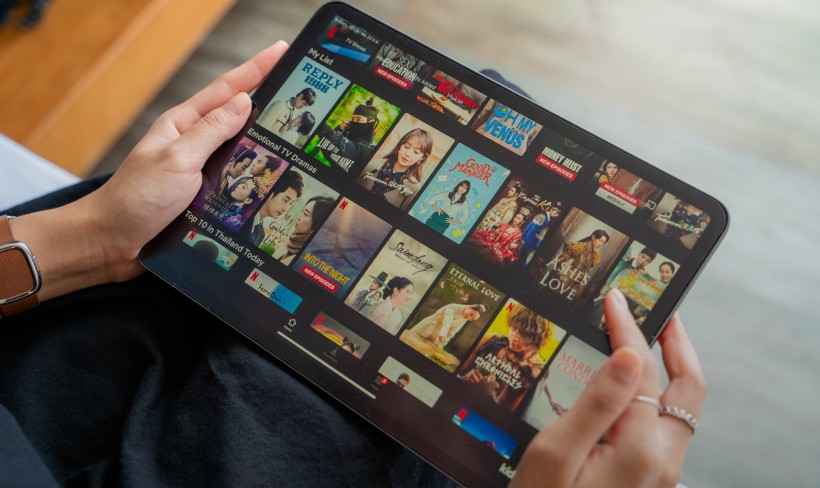
Media & Entertainment
OTT Platform
Ad Tech
5 minutes to read
Pluto TV—a free streaming TV service owned by Paramount Global
In 2017, we kicked off our journey with Pluto.tv by bringing on board top-notch engineers to kickstart our development teams and lay the groundwork for Pluto.tv's bright future.
Learn more
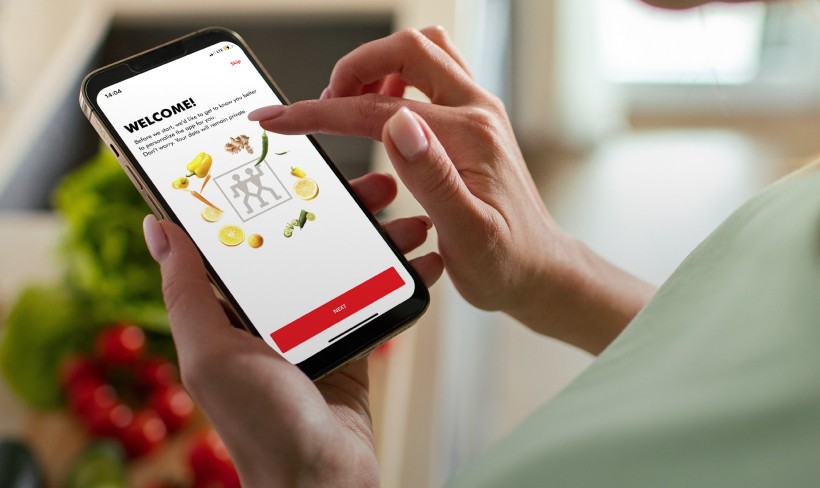
Manufacturing
E-commerce
IoT
4 minutes to read
ZWILLING—a renowned brand in crafting high-quality kitchenware
In May 2021, we began working with ZWILLING to develop stable and user-friendly native Android and iOS applications for their innovation department.
Learn more
Find a case similar to yours
Uncover relevant case studies with our powerful search and tagging system.
Search…
Media & Entertainment
E-commerce
FinTech
Hospitality
Renewable Energy
Real Estate
Airlines
Logistics
Manufacturing
Data Analytics

Airlines
Cloud
AI
8 minutes to read
Airport Baggage Handling System: Engineering for Mission-Critical Reliability
A major Eastern European international airport, serving millions of passengers annually, faced a significant expansion challenge. The addition of a new terminal required a state-of-the-art baggage handling system that could operate flawlessly from day one.
Learn more

FinTech
QA
UI/UX Design
5 minutes to read
Digital audit platform
Brightgrove has partnered with a German-based company which provides Digital Audit Platform to 500+ audit, financial and professional firms. The main goal of the platform is to speed up the Balance Confirmation request process for Audit providers and their clients.
Learn more

Hospitality
AI
Microservices
4 minutes to read
5S Scenario Builder. Corporate Hotel Program Optimization
The strategic hotel selection process required processing vast amounts of historical booking data across thousands of hotels and evaluating hundreds of potential hotel combinations for each city.
Learn more

Data Analytics
Cloud
REST API
8 minutes to read
Coginiti—Data Analytics Management Software
Since 2012, Brightgrove has maintained an enduring partnership with Aginity (now Coginiti), the management company through multiple transformative phases.
Learn more

Manufacturing
IoT
Cloud
7 minutes to read
IoT Solution for Industrial Tools Manufacturer
Our client, a global leader in industrial tools and automotive components manufacturing, sought to integrate Internet of Things (IoT) capabilities into their product line, transforming traditional industrial tools into smart, connected devices.
Learn more

Renewable Energy
Cloud
Microservices
7 minutes to read
Cloud-Based Asset Management for Renewable Energy Plants
For this project, Meteocontrol wanted to develop a cloud-based asset management platform (mc Assetpilot) that could optimize renewable energy operations, streamline financial tracking, and enhance operational decision-making.
Learn more

Logistics
QA
REST API
6 minutes to read
PIN Mail AG. Leading German correspondence delivery company
Founded in 1999 in Berlin, PIN Mail AG is a leading German correspondence delivery company with over 1,300 employees.
Learn more

Logistics
Cloud
REST API
5 minutes to read
IoT-Connected Car Tracking Mobile Applications for Fleet Management
A leading German manufacturer of car tracking devices, specializing in onboard diagnostics (OBD) solutions, sought to enhance its vehicle tracking and trip logging capabilities through connected mobile apps.
Learn more

Manufacturing
REST API
Cloud
6 minutes to read
Legacy ERP System Redevelopment for an Industrial Equipment Manufacturer
When a leading German industrial equipment manufacturer found their 70-year legacy hampering growth, they turned to Brightgrove for a solution.
Learn more

Manufacturing
IoT
SAP
6 minutes to read
Machine Vision Solution for Industrial Manufacturing
The company aimed to standardize its software solutions across all business units, ensuring scalability, efficiency, and uniformity.
Learn more

Real Estate
SAP
Mobile
4 minutes to read
Promos—Real Estate CRM
A leading German real estate software company with a €32 million annual revenue and over two decades of market leadership faced the challenge of finding SAP developers who also understand mobile development.
Learn more

FinTech
Cloud
Microservices
5 minutes to read
UK-based payment solution provider expanding to continental Europe
Brightgrove has partnered with an ambitious UK-based company to extend their cloud-native payment solution platform.
Learn more

Hospitality
UI/UX Design
QA
5 minutes to read
Digital Transformation of Commission Collection for a Global Hotel Supplier
Our team was engaged by a global hotel supplier to implement the "Paywall" initiative – a comprehensive digital transformation of their commission collection process.
Learn more

Hospitality
REST API
Cloud
4 minutes to read
RESTification — Process Access to REST APIs for Partners
An organization undergoing modernization needs to manage and secure access to its REST APIs for external partners.
Learn more

Media & Entertainment
SaaS
Microservices
8 minutes to read
Planeta Kino Digital Transformation: A Multi-Platform Success Story
This comprehensive transformation involved modernizing multiple customer-facing platforms while maintaining business continuity for their cinemas network and premium viewing experiences.
Learn more

Hospitality
Cloud
Microservices
6 minutes to read
API-First Architecture Implementation for a Global Hospitality Tech Platform
The client faced critical scalability challenges during peak travel seasons, potentially risking up to €800K – €1M in lost bookings during high-demand periods. Their legacy booking system, built over 10 years ago, struggled to handle modern integration requirements.
Learn more

Real Estate
Cloud
Microservices
3 minutes to read
Real Estate platform Upgrade
The real estate platform serves as a backbone for the day-to-day real estate broker operations as well as provides overview and detailed reports on the past and current real estate market state.
Learn more

Hospitality
Cloud
UI/UX Design
6 minutes to read
Procurement Platform Interface Modernization from JSF to React
The HRS eRFP platform, also known as the HRS procurement or sourcing platform, is a comprehensive solution developed by HRS Group to streamline corporate hotel procurement processes.
Learn more
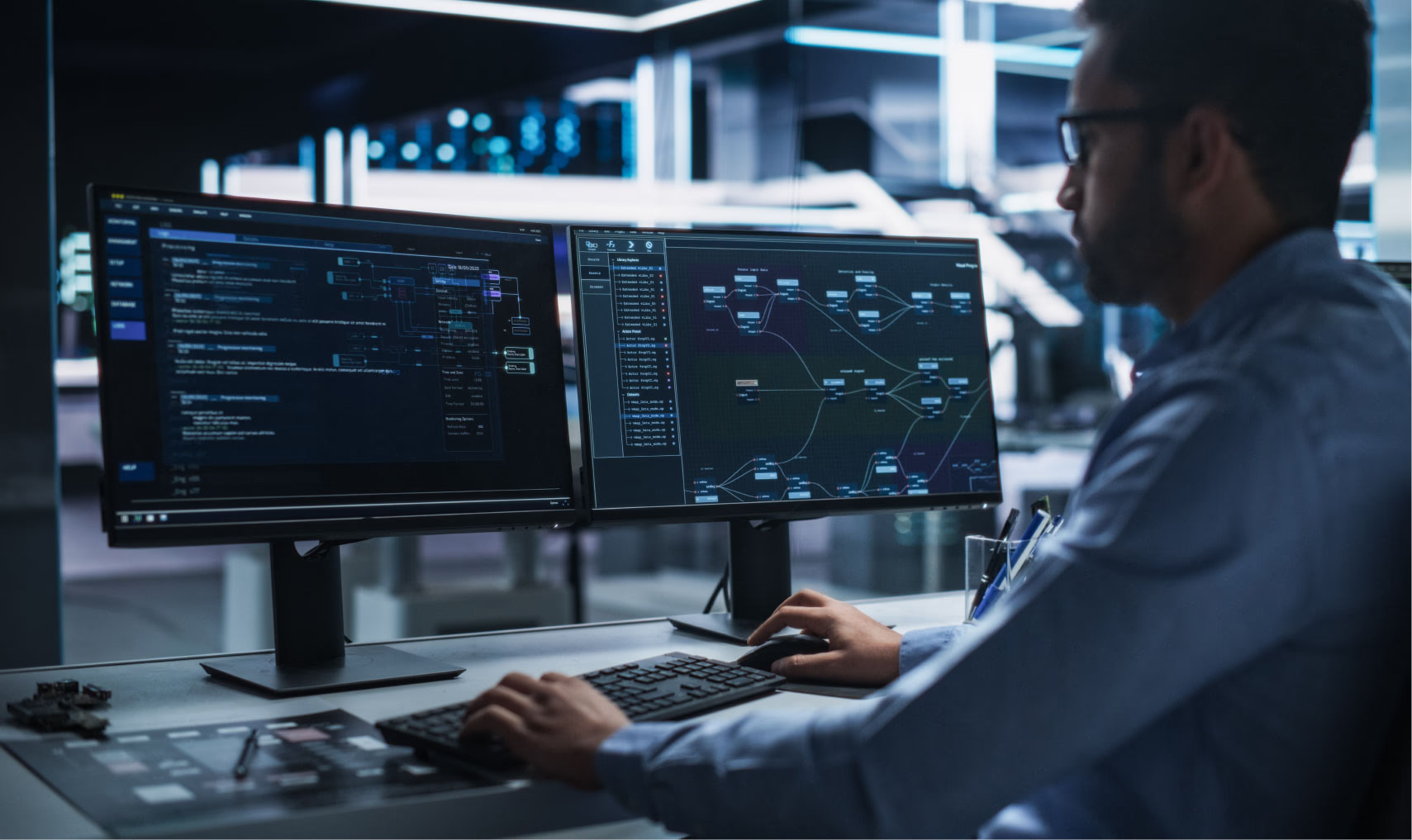
Hospitality
Cloud
AWS
5 minutes to read
Large North-American Travel Tech Booking Engine Modernization
An enterprise-scale leisure travel marketplace connecting travel agents with leisure-focused travel suppliers, facilitating research, marketing, and selling of vacations in the USA and Canada.
Learn more

Renewable Energy
UI/UX Design
Microservices
6 minutes to read
From Raw Data to Interactive Visualization for Solar Monitoring System
In 2012, solar monitoring systems were primarily data-driven, offering raw data outputs with minimal visual representation or integration. Operators struggled with scattered screens and single-purpose tools.
Learn more

Hospitality
FinTech
Cloud
8 minutes to read
Successful integration cases across different domains
The following use cases demonstrate our ability to tackle integration challenges of varying complexity across different business domains.
Learn more

Hospitality
Microservices
Cloud
5 minutes to read
Solving Integration Problems in Travel Tech
We partnered with a global travel technology company to overhaul their fragmented systems through advanced integration services.
Learn more

Hospitality
Cloud
SaaS
4 minutes to read
Collaborative SaaS Transformation of a Global Travel Technology Platform
Faced with rising AWS costs, a top-three European hotel portal and global business travel leader required a comprehensive cost optimization strategy
Learn more

Hospitality
Cloud
AWS
3 minutes to read
Cloud transformation—AWS cost optimization
Global hotel solutions provider, ranking among the top three hotel portals in Europe faced challenges with escalating AWS costs and had to define and implement a comprehensive cost optimization strategy.
Learn more

Hospitality
Google Cloud
Azure
3 minutes to read
Cloud migration—cloud to cloud—Lift & shift—GCP to Azure
On our tech exploration journey, we discovered an innovator rooted in a thriving metropolis, a beacon of forward-thinking and adaptability in the tech realm. Their location, pulsating with life and dynamism, seemed symbolic of their approach: always moving, always evolving.
Learn more

FinTech
Microservices
AWS
3 minutes to read
Cloud migration—cloud to multicloud
In a dynamic marketplace, this platform stands out, offering a seamless, enriching shopping experience.
Learn more

Media & Entertainment
Cloud
AWS
4 minutes to read
Cloud migration—monolith to cloud
Free ad-supported streaming television (FAST) service owned and operated by the Paramount Streaming division of Paramount Global.
Learn more

Hospitality
Cloud
Microservices
3 minutes to read
HRS GROUP—a global tech company focusing on business travel
HRS Group is a global tech company focusing on business travel, ranking among the top three hotel portals in Europe and as a market leader in the global business travel sector.
Learn more

E-commerce
UI/UX Design
Computer Vision
4 minutes to read
AI Powered Amazon Recommendation Engine
The client needed a smart solution that could analyze thousands of Amazon marketplace products to identify optimization opportunities.
Learn more
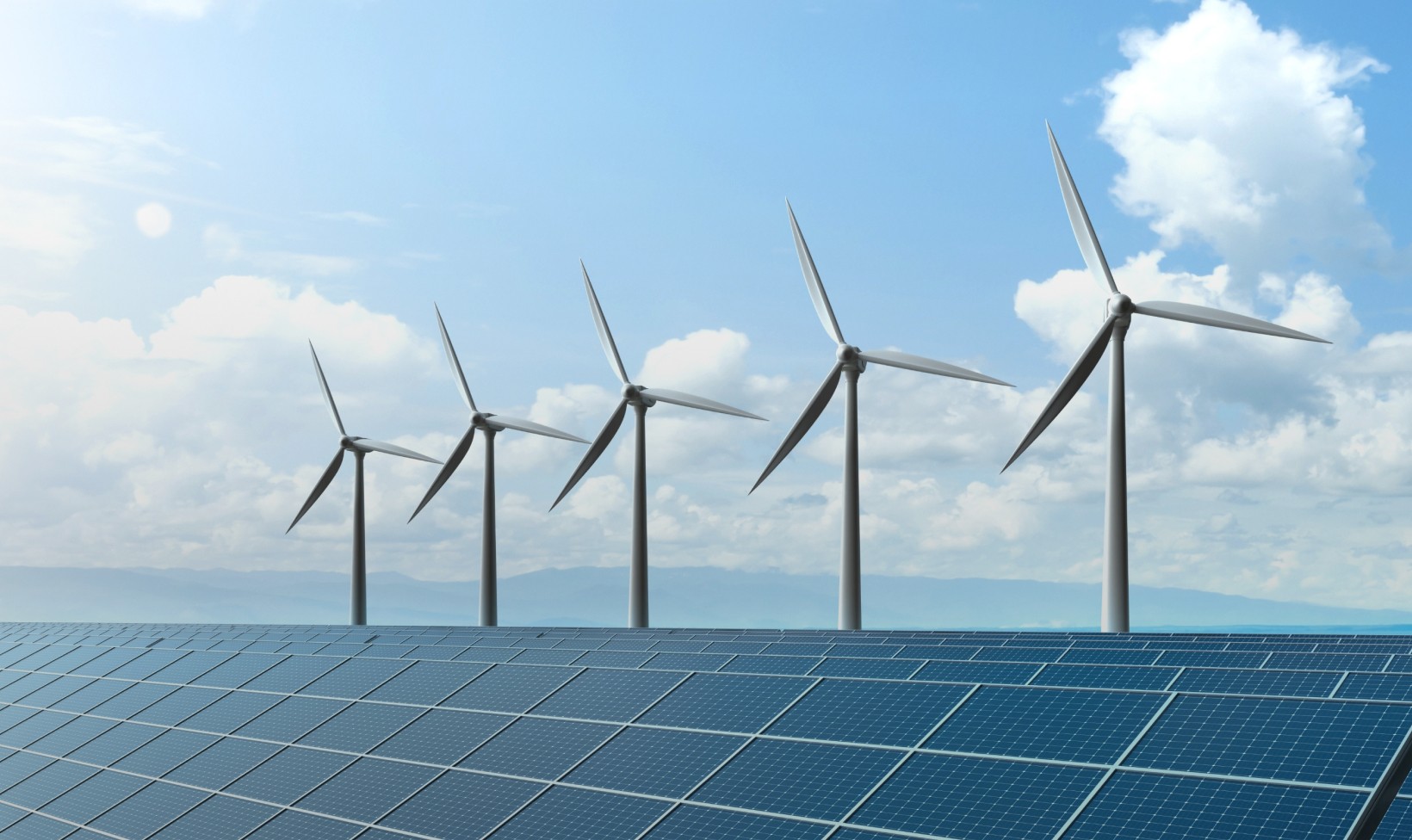
Renewable Energy
SaaS
Google Cloud
4 minutes to read
CerQlar—renewable energy trading and certification platform
In 2021, we partnered up with CerQlar, a Dutch company setting new energy attribute certificate trading standards in Europe.
Learn more

Real Estate
AI
Cloud
4 minutes to read
Modernizing New York's Real Estate Technology Platform
In 2014, we started one of our most long-running projects with a client, a US real estate agency turned digital leader in its industry.
Learn more
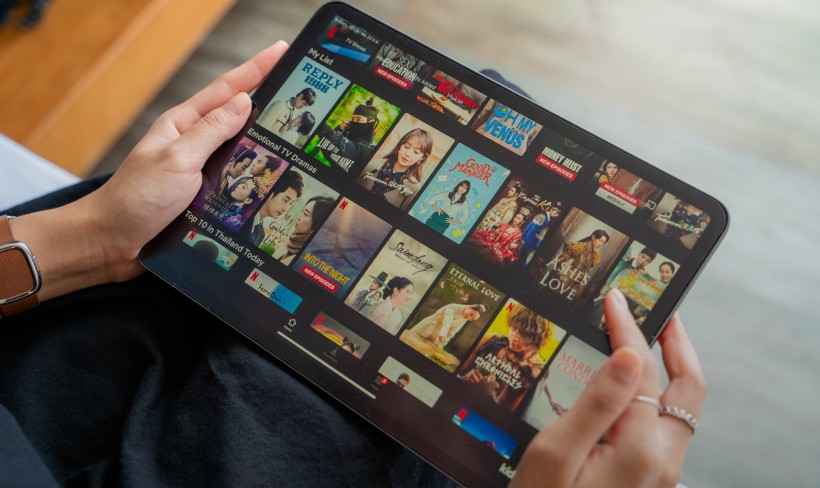
Media & Entertainment
OTT Platform
Ad Tech
5 minutes to read
Pluto TV—a free streaming TV service owned by Paramount Global
In 2017, we kicked off our journey with Pluto.tv by bringing on board top-notch engineers to kickstart our development teams and lay the groundwork for Pluto.tv's bright future.
Learn more
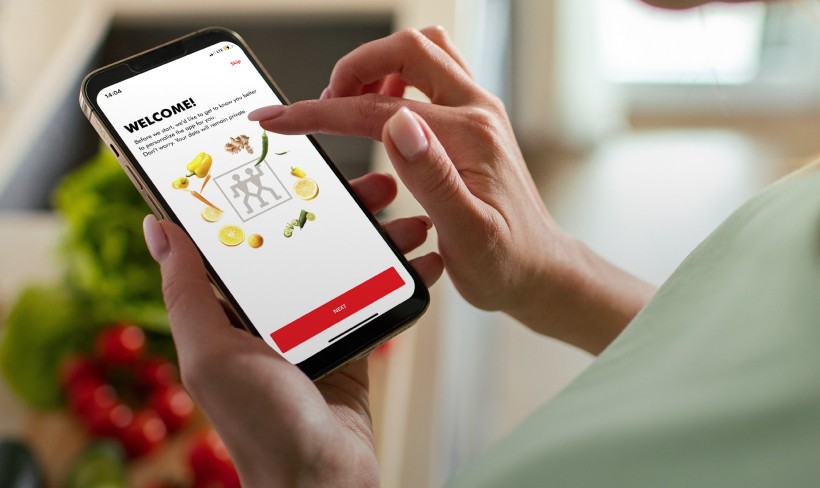
Manufacturing
E-commerce
IoT
4 minutes to read
ZWILLING—a renowned brand in crafting high-quality kitchenware
In May 2021, we began working with ZWILLING to develop stable and user-friendly native Android and iOS applications for their innovation department.
Learn more
Let's connect!
Contact us
Reach us today to learn more about our services and how we can help your business evolve
Trusted by
Let's connect!
Contact us
Reach us today to learn more about our services and how we can help your business evolve
Trusted by
Let's connect!
Contact us
Reach us today to learn more about our services and how we can help your business evolve
Trusted by
Let's connect!
Contact us
Reach us today to learn more about our services and how we can help your business evolve
Trusted by
Services